WHITEPAPER |
How to prevent the last errors when implementing and using automation in your warehouse
Automation like mini load cranes, picking robots, pater noster systems, shuttles, is known to power up warehouse efficiency. But – and this is important – it in general doesn’t make logistics flawless.
Although one of the advantages of automation is to reduce the risk of human mistakes, using automation is not a guaranteed quick fix to have zero errors. We repeatedly see examples of irregularities occurring in automation solutions. Read to explore why this is, and how intelligent video analysis can assist you in reaching flawless logistics.
Part 1: Make implementation of automation smoother
Implementing new automation is a complex project. Business logic, data quality, system integrations, user interfaces, work routines and training are some of the many aspects you need to take care of to make it a success full project.
The stakes are high, and hiccups will occur. By using intelligent video analysis during the implementation, you will have visual proof of exactly what happened. It saves valuable time when troubleshooting and significantly lowers the number of assumptions in your project. Implementation becomes smoother with visual insights instead of assumptions and best guesses.
Using searchable video during the simulation phase, as well as in the ramp up phase, makes the trouble shooting significantly simpler and less time consuming. In addition, having visual insight reduces risk. Time is money – a delayed go live can cost a lot.
Part 2: Get control of the critical human machine interactions
Almost all automation solutions are still surrounded by tasks performed by us humans. Often manual work occurs when goods change ownership. Examples are:
- Decanting goods into automation
- Picking and packing
- Transport consolidation from automation
These are critical processes where errors often occur. Use intelligent video analysis to quickly find out the root cause of an error. The related video stream will show you whether to adjust the system or the manual instructions.
Example:
With automation in a Goods-To-Person process, often only the picking location is presented to the operator. He or she will confirm the picking activity, regardless of the goods.
Small goods are often stored in bins with several compartments. An automated warehouse might make use of thousands of bins. And it’s not unusual for a bin to have up to 16 compartments.
This makes decanting a critical part of goods handling. If goods is accidentally put in the wrong compartment or bin, it’s a demanding task to locate it and correct it. One error in decanting may multiply into numerous picking errors. Most often an error in decanting doesn’t reveal itself until customers start complaining. Measures must be taken to stop the error from happening over and over again.
With intelligent video analysis you can easily travel back in time, to investigate what exactly happened. You can, for example, immediately retrieve the video clip of that specific inbound order number, or the bin number or the article number and instantly start investigating the root cause of what went wrong. Once found, corrective measures can be taken.
Part 3: Have ongoing control in critical areas
In an automated warehouse, buffer zones, accumulation zones, exception zones, consolidation areas and more are well-known critical areas. Here goods often get lost due to one or many reasons including the very basic error that goods are misplaced in, or outside of, the right zone.
Making use of intelligent video analysis in critical areas in your automated warehouse can bring several benefits. First, video can warn you that something is not going as expected (and you instantly see what is going on). Searchable video can help you in seeing what happened and find the right information on which the processes can be finetuned, to prevent hiccups in these critical zones.
Part 4: Control inventory in a smarter way
In all warehouses, sooner or later, someone will be asked to check the inventory of a specific item in the automation system. The warehouse needs the correct stock balance. But where to start?
The reality is that a misplaced item could be in any of the thousands of locations inside the automation system in use. It normally is a time-consuming task to detect and correct this kind of errors. Not any longer with searchable video. The platform enables you to search, see and act, instead of “going fishing” to find the missing link. You can use searchable video to find over deliveries too.
Take action to prevent errors in automated goods handlingWhitepaper by:
Staffan Persson, logistics expert, Global PreSales Director and co-founder SiB Solutions
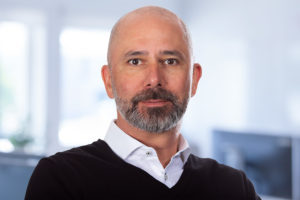
Staffan Persson, SiB Solutions